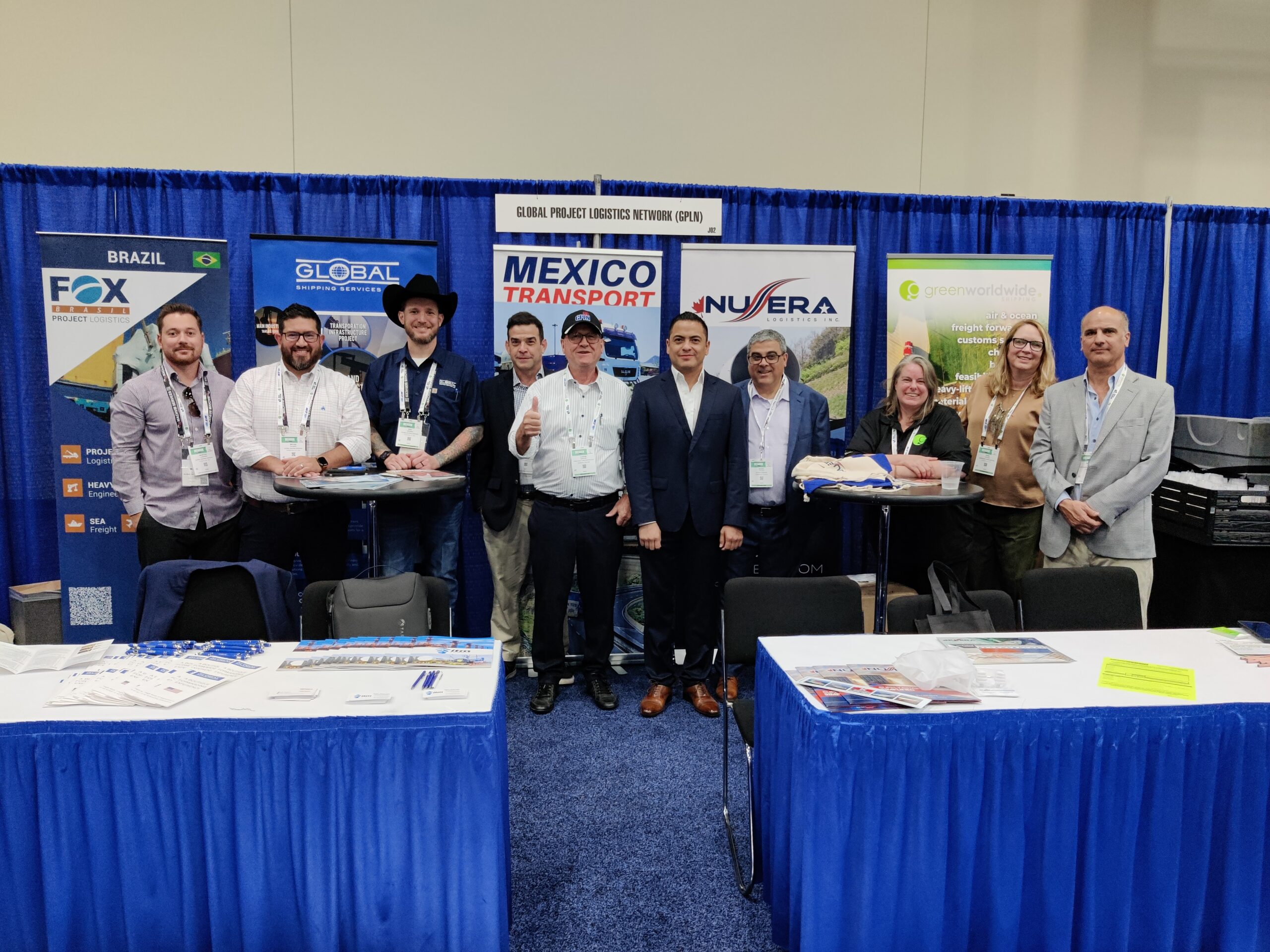
A word from GPLN: Newsletter Issue 94 / September-October 2023
Dear Reader,
Breakbulk Americas in Houston was a huge success and posted the best results in their 34-year history with 5,665 attendees. GPLN was also part of it and all GPLN companies exhibiting at our stand were very pleased with the outcome. One of the participants at our stand, Murilo Caldana, project director at FOX Brasil, did also moderate the “Latin America Spotlight: Outlook, Projects and Opportunities” session. He said that “energy, mining, and infrastructure are taking up the biggest share of megaprojects currently under construction and the region is tipped for huge growth in the renewables sector, particularly offshore wind and hydrogen,” He also noted that “The decommissioning market is on the rise and alongside this, large scale port development to service the needs of the region’s projects”. In Brazil, Latin America’s largest economy, hydrocarbons, renewable energy and pulp and paper continue to represent the fastest-growing sectors for breakbulk. Mexico, meanwhile, is gearing up for more investment amid nearshoring from China. Some 400 US and Asian companies are interested in relocating to Mexico by 2024, generating some 700,000 jobs, while nearshoring could boost the country’s GDP by US$50 billion over the next six years.
Future downstream oil and gas industry investment is likely to be increasingly focused on sectors like hydrogen, biofuels and petrochemical production to support the energy transition, alongside traditional oil refining and liquefied natural gas (LNG) activities. This increase in project logistics and heavy lift demand will put further pressure on logistic companies. Jigar Shah, director projects & 3PL of GPLN member JSL Global in Qatar and Oman, which provides logistics services to oil and gas industry companies and the chemicals sector, including the storage of shipments at its dangerous goods warehouses in Qatar and Sohar, Oman, provided a specific example of the growing international interest in biofuel and related new projects. “The Qatar Investment Authority is considering investing in a green hydrogen and ammonia project in the Suez Canal Economic Zone in Egypt which is positioning itself as a regional hub for green energy,” he pointed out. “International companies have signed USD33 billion worth of preliminary agreements for green ammonia and hydrogen projects this year.” After the record-breaking attendance of our AGM in Rotterdam in June 2023 with over 210 GPLN delegates, our next annual global conference will take place at the Hilton Hotel in Den Haag from Mai 18-20, 2024. Right after our AGM, on May 21, 2024, our renown Heavy Transport and Lifting Seminar will take place at the same venue which is also open for non-members. More details and delegate registration for both our AGM and Seminar are available on our dedicated websites. These GPLN events can be combined with Breakbulk Europe which follows from May 21-23, 2024 at Ahoy Convention Center Rotterdam. GPLN will exhibit at this event and has secured a prime location in the main hall with a 36 sqm booth (#1A20) which is the equivalent to 4 regular stands.
The GPLN team will exhibit next year also at Breakbulk Middle East in Dubai from February 12-13, 2023 at Dubai World Trade Centre, together with several GPLN members. Please visit our GPLN Booth #E02 which is located next to the main entrance.
Best regards,
Your GPLN team
Lysander and Khedivial in Successful Alliance
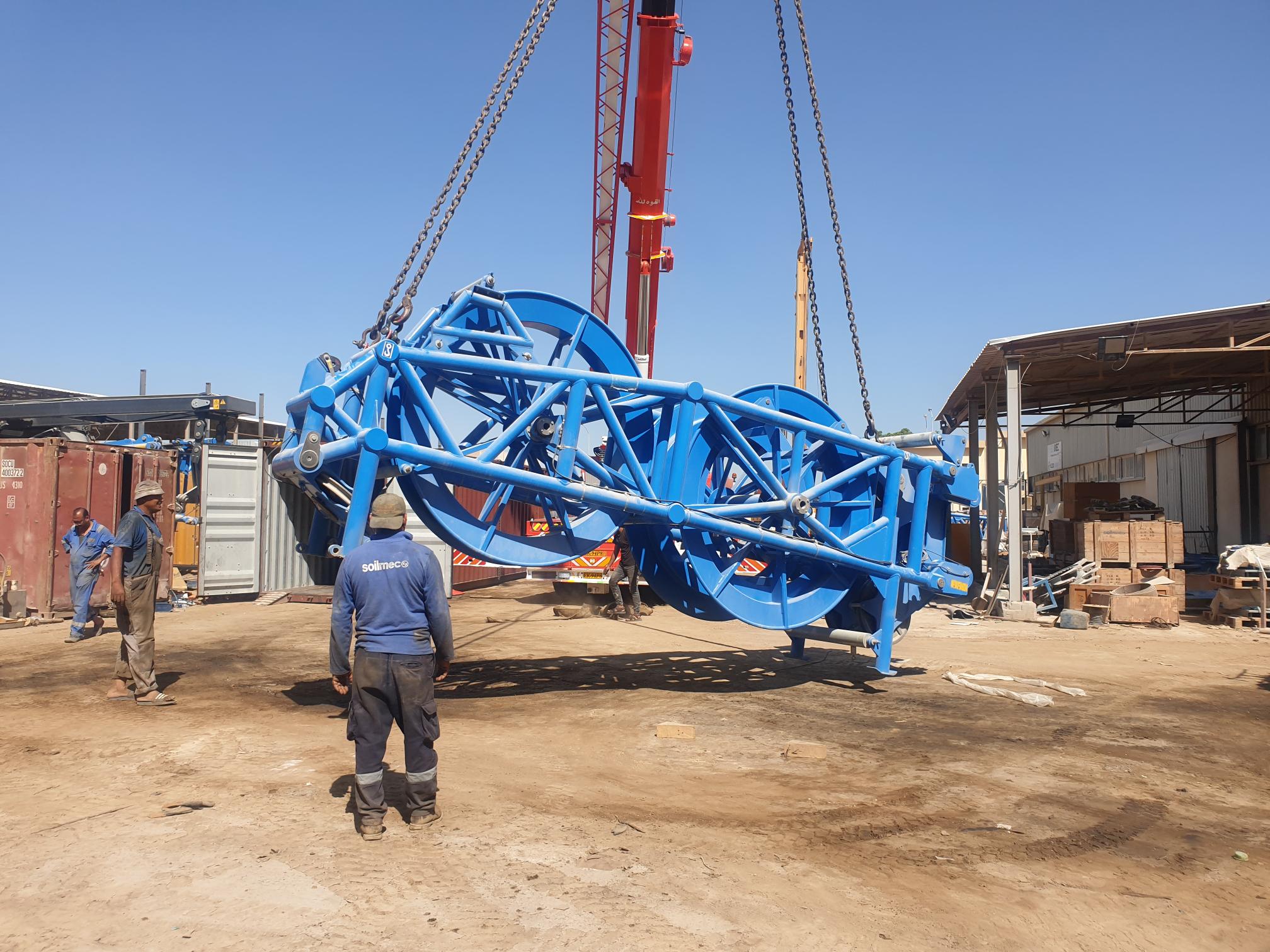
GPLN member Lysander Shipping from UK undertook recently an important project for one of their prime Italian customers and chose to nominate their excellent GPLN partner, Khedivial Marine Logistics from Cairo, Egypt, to assist. Together they collaborated to move a Pile Driver and Parts from collection at shipper’s factory in Egypt for loading on board a vessel in Port Said to Manila, Philippines. The cargo consisted of many various heavy and out of gauge pieces, with the heaviest weighing 55 tonnes. Direct delivery up to under hook vessel was carefully planned and co-ordinated between all parties successfully and cargo was delivered together and on time.
New GPLN Members Issue 94 / September – October 2023 |
||
Germany | Düsseldorf | PNS Project GmbH |
Qatar | Doha | Milaha Maritime and Logistics Integrated W.L.L. |
Singapore | Singapore | Bruhat Logistics Pte Ltd |
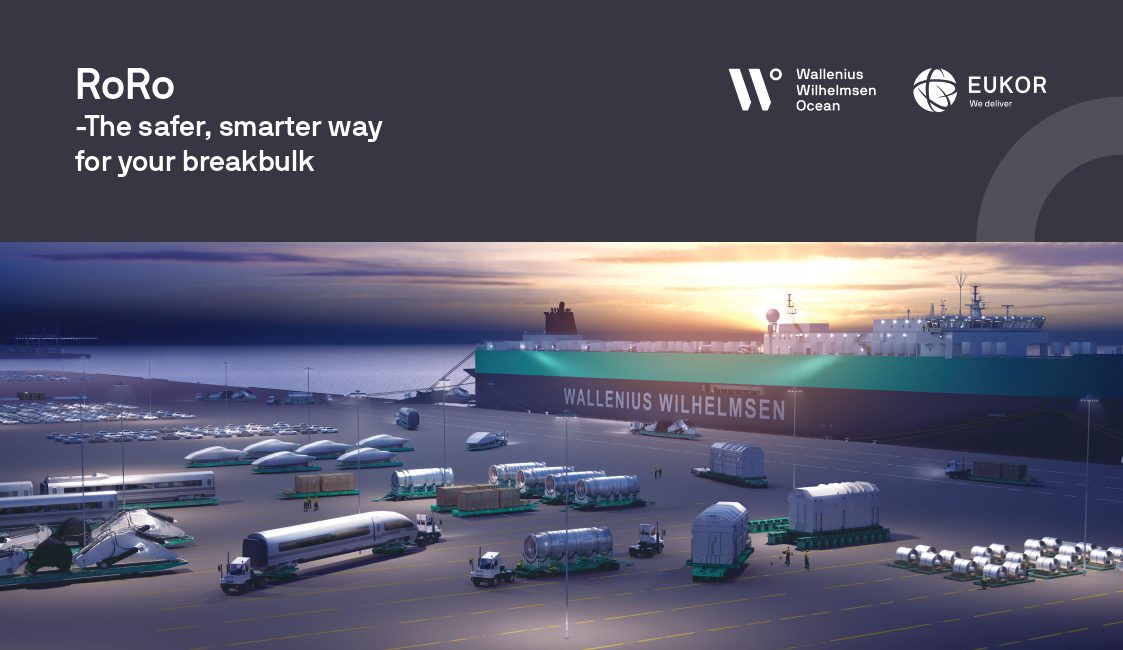
3p logistics handle special project from China to Sweden
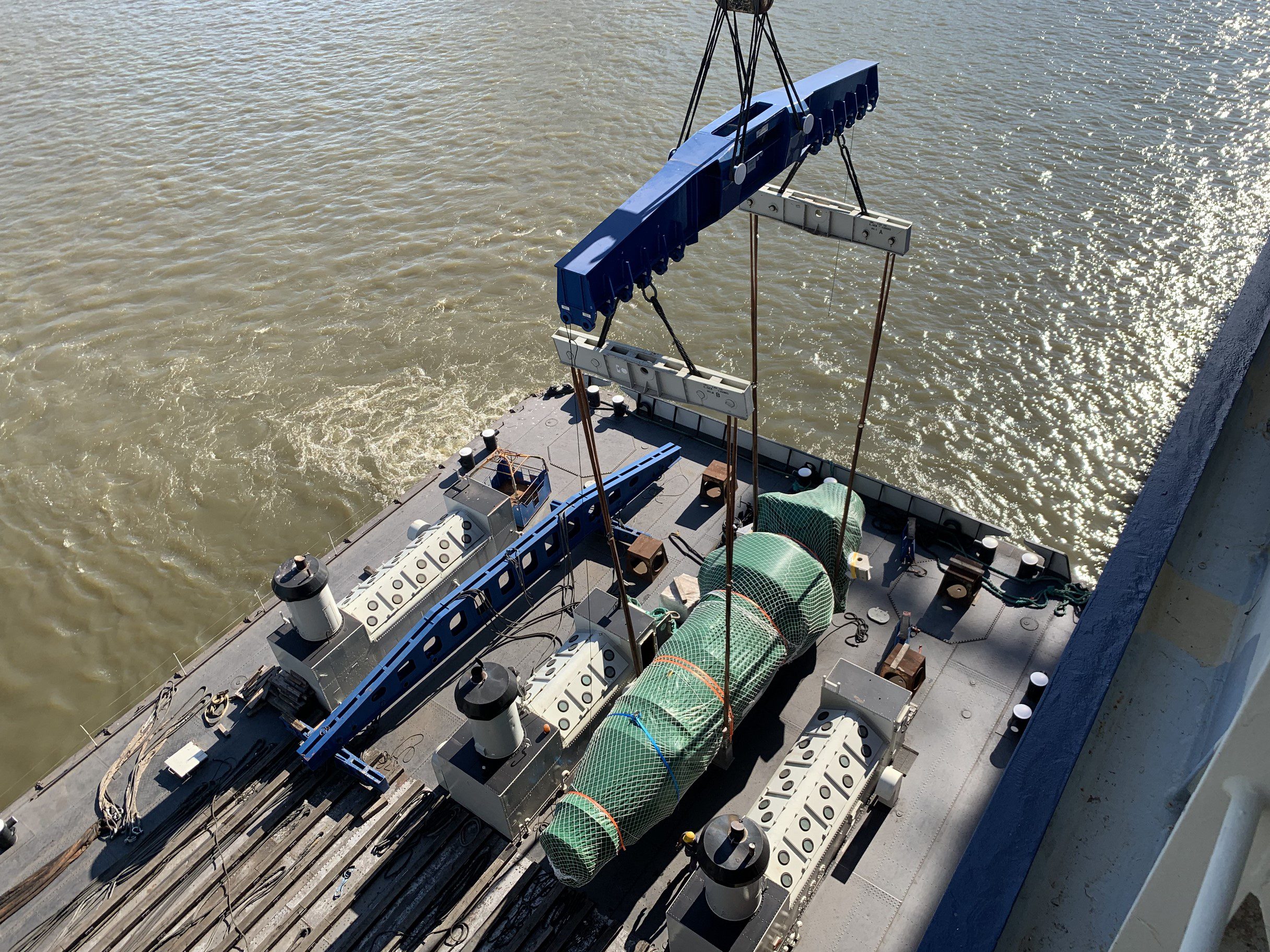
GPLN member 3p logistics (3PL) from Denmark handled recently an extraordinary project from China to Sweden for a new green tech manufacturer of the world’s most environmentally friendly mineral fertilizer. The Swedes will manufacture a sustainable mineral fertilizer from residual products, from electric car battery manufacturing and the pulp industry. They will use traditional and proven process technology powered by fossil-free electricity. The product, potassium sulphate, will be an important contribution to the green transformation of agriculture. And it is an honor for 3p logistics to be a part of the unique project. Also, future production plants are planned to be in Örnsköldsvik and Skellefteå, as well as additional production plants in the Nordic region and USA.
The cargo had a really huge size with 7.4 m diameters.1 giant Crystallizer had the size equal of 24 standard containers on containerized vessel! There were 2 huge breakbulk items + 7 OOG items. This was a one of the biggest (height and width) items in 3PL history (not heaviest or longest). The height was almost 7 m and the width 7.4 m. From China we were using an ocean containerized vessel to Hamburg. We were using a floating crane for unloading from the containerized vessel and loading and to the barge to delivery between the terminals in Hamburg. There we arranged a special extraordinary permit for our ship. Then the goods were transloaded to our breakbulk vessel in Hamburg and delivered to the destination in Sweden.
3P Logistics Project department: Group Project Director Niels Chr. V. Andersen and Global Project Manager Ilya Goncharov successfully prepared, coordinated, and completed this delivery starting from the first touch.
Total Movements handle Multimodal Project
GPLN member Total Movements from India successfully handled a multimodal (road + barge) movement of lengthy columns for an export Fertilizer Project. This heavy lift transportation involved moving a 41-metre-long / 680 MT Ammonia Converter and a 30-metre-long / 380 MT Ammonia Unitized Chiller from the supplier’s factory to the load port by multi-modal transportation. Road transportation from the supplier’s factory to the nearest jetty, rolling-on the two lengthy columns onto the barge, coastal movement to the final load port on the west coast of India and feeding alongside the vessel were all part of our scope.
Major features involved in the challenging move were:
Felicitous vehicle configuration / Transporting with civil work enroute / Rolling-on and securing the cargo on the barge meeting the short tide window / Double banking operation at Mumbai port. Both these units were safely delivered at the Indian loading port by Total Movements for further shipping to its destination. All the cargo was delivered in a safe and timely manner, much to the delight of our customer. We’d like to express our gratitude to all the stakeholders who supported us in making this shipment a huge success.
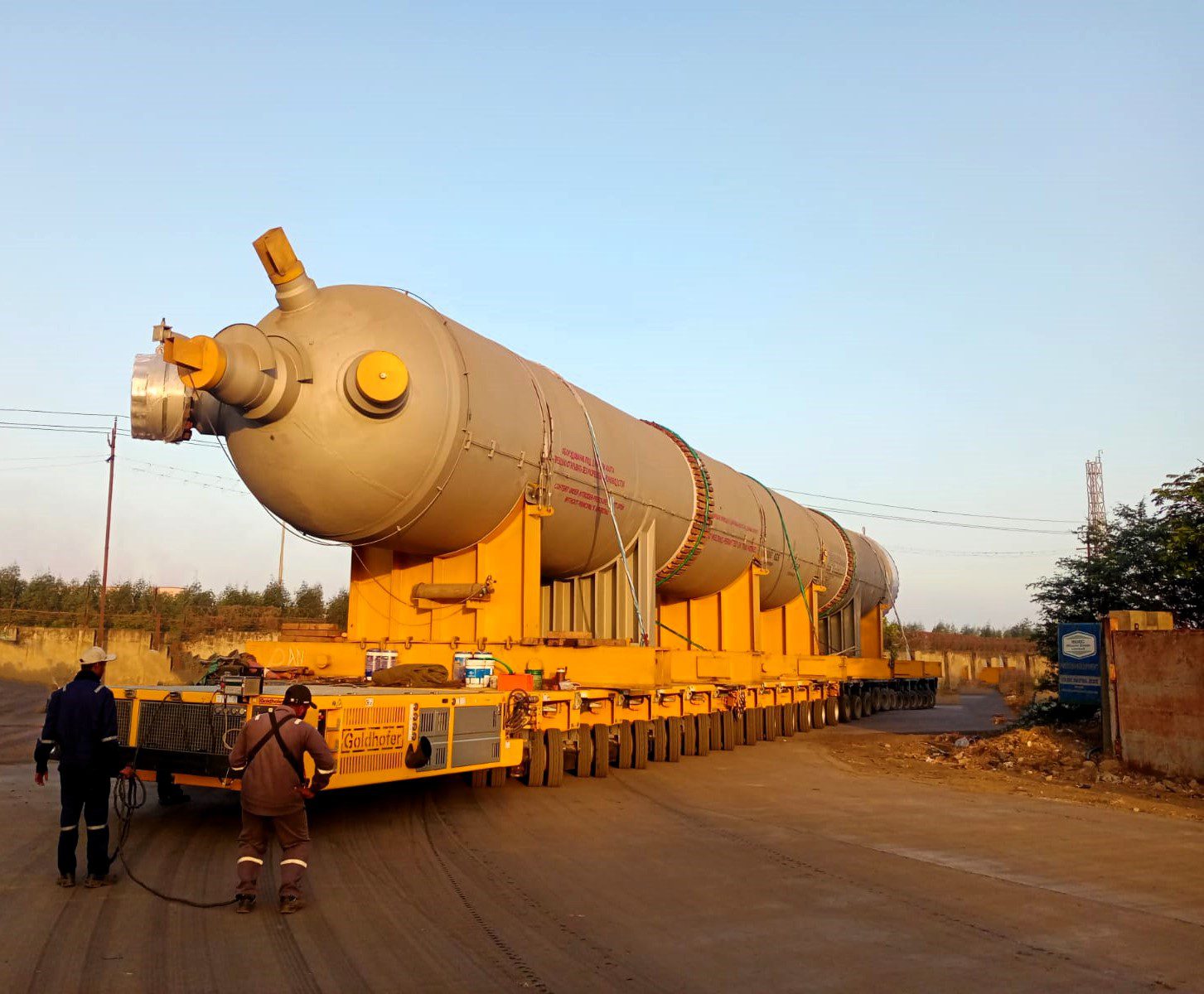
PROTRANSER handles multiple tasks
![]() |
![]() |
© Protranser International Logistics Co., Ltd. All rights reserved
GPLN member Protranser from China delivered a mobile crane and accessories from Qingdao, North China to Durban, South Africa by Breakbulk vessel. The total volume was 14 packages / 162,739 kg / 267.11 CBM. The weight of the heaviest unit was 74 MT. Working scope was chartering service for the breakbulk vessel.
Protranser’s team delivered also 2 excavators from Tianjin, North China to Monrovia, Liberia by sea. All cargo was loaded on 2*40’FR + 1*40GP.
Furthermore, Protranser delivered 400+ CBM equipment from Tianjin to North America. The total volume was 73 pieces / 80,810 kg / 412 CBM. Working scope included picking up cargo from the factory located in Anshan City, Liaoning province, North China, 630km away from Tianjin port, port service in Tianjin port and chartering service for the breakbulk vessel.
Atlas Shipping Services handle Air Charter
GPLN member Atlas Shipping Services Pvt Ltd from India recently secured a contract for the air export of a Power Transmission Project. The project involved transporting equipment for the construction of a 33 KV Power Transmission Line and distribution network project in Congo. This project was commissioned by the Ministry of Energy and Water Resources, Government of the Democratic Republic of Congo (DRC).
The shipment originated from Mumbai Airport and was destined for Kinshasa, Congo. The total weight of the shipment amounted to 90,700 kilograms, and it was efficiently loaded onto a B747F aircraft and dispatched as a single consignment.
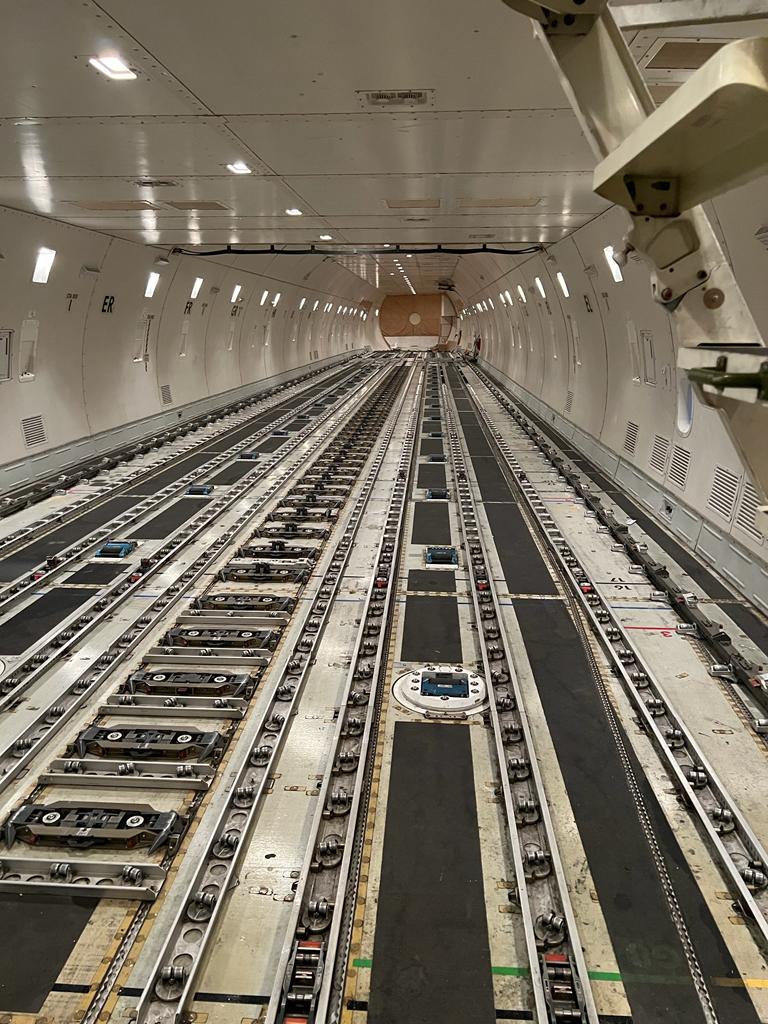
This remarkable achievement marked Atlas Shipping Services Pvt Ltd.’s inaugural air charter for a project cargo. The team executed this complex operation with great success, showcasing our expertise in handling such specialized logistics challenges.
Zenith manage to move Oil processing equipment
GPLN member Zenith from UK successfully supported their client in moving oil processing equipment from the factory in China to door delivery in UK. The move comprised of 6 units totalling 120,940 kg / 774 CBM. Due to the lack of breakbulk vessel availability for direct shipment from China to the UK, the best route available was to move the cargo from Zhangjiagang in China to Antwerp, Belgium and then from Antwerp to the UK via barge into Tilbury. Once in Tilbury the next challenge was moving the loads to their final delivery location in Kent. This required the goods to be moved across the Thames River via the busiest bridge crossing in the UK and transporting this OOG equipment over the bridge would involve having the crossing closed to general traffic for the duration of the move. For several weeks Zenith worked together with the British Transport authorities and the police to arrange movement permits for private escorts of vehicles, and polices escort vehicles in regards to the physical closure of the Dartford crossing to general traffic for an allotted period of time. Due to the size of the cargo, the authorities would only allow transportation of 2 units in any one movement, so Zenith eventually agreed with the authorities to have the bridge closed to general traffic for 2 hours from midnight until 2am on three consecutive nights (Friday, Saturday, Sunday) to allow the cargo to cross. The operation went perfectly and the client was extremely pleased to receive all 6 of their units waiting for them on site on the following Monday morning.
![]() |
![]() |
SCT Logistics handle steel structure project
GPLN member SCT Logistics from Vietnam was awarded by its client in Thailand to handle a steel structure project shipment from Hai Phong to Puerto Angamos in Chile.
This cargo was shipped to Chile for construction work. The project started in DEC 2022 and was completed in MAY 2023. STC and our partner successfully handled the cargo from the factory to delivery on-site in Chile. There was a total of 137 x 40 open-top containers with a volume of 46 x 40OT (IG) & 91 x 40OT HC (IG) (combined between 40OT & 40 OT HC). This cargo was shipped to Chile for construction work. SCT Logistics was responsible for cartage in Hai Phong, marshaling the equipment with carriers to catch the loading plan from the shipper (including re-position EQ from others), haulage empty and laden containers, ocean freight, fumigation on wooden products and export customs clearance in Vietnam. Besides, we also supervised the loading and lashing of cargo on containers to improve safety before transportation. These 137 containers were divided into 13 lots with different sizes for each shipment depending on the shipper’s packing plan. However, we still met the quantity of equipment required by the customers, and reached per shipment up to 20-23 x 40ft open-top containers.
Furthermore, SCT handled recently also a crane and spare parts project shipment from Ho Chi Minh City in Vietnam to Mumbai in India and is proud to have successfully transported OOG shipments by breakbulk vessel. Scope of work: Custom Clearance / Supervising (pre-loading, loading, lashing) / Handling to port charges at POL / Delivery from Ho Chi Minh to Mumbai port by break bulk vessel (FILO term). Commodity: Crane and spare parts. Quantity: 111 packages. Volume: 1251.5MT / 3260.8 CBM
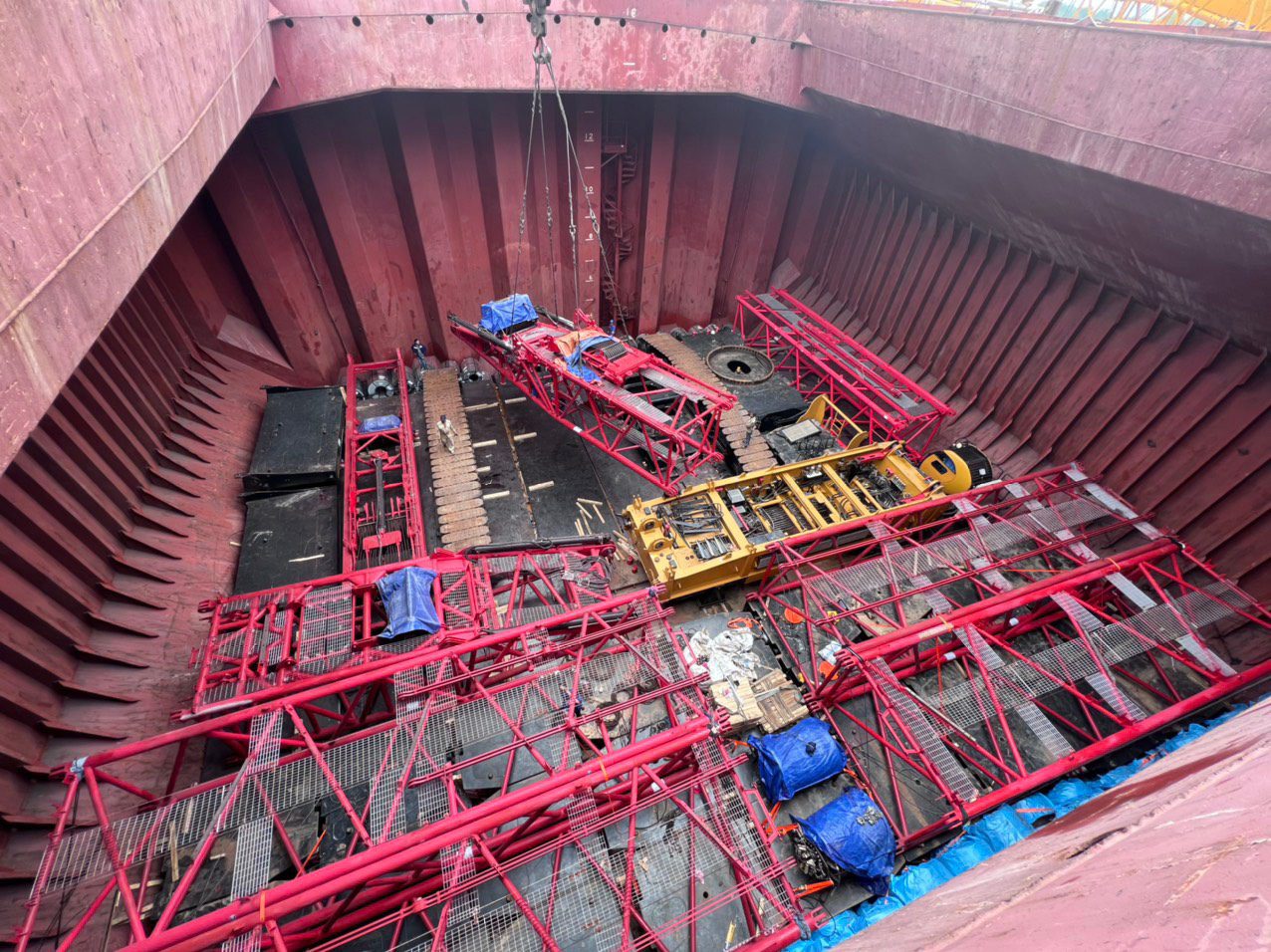
Fleet Line Shipping (FLS) Join Forces for a Remarkable Feat
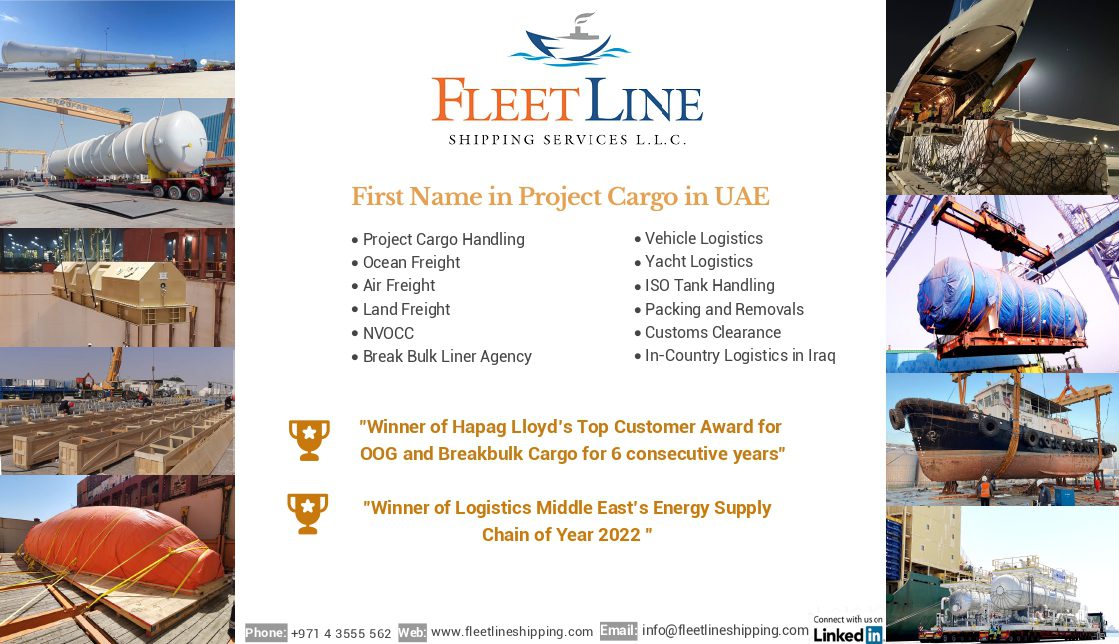
In another incredible collaboration, Maersk and GPLN member FLS Dubai have successfully achieved the impossible by loading a 41-ton Coiled Tubing into a heavy-duty 40’ Flat Rack container, pre-lashed and safely loaded from Jebel Ali to Europe. What makes this accomplishment even more astonishing is that the Coiled Tubing, with a length of only 4 meters, posed a unique challenge.
FLS’s ingenious solutions involved redistributing the concentrated weight across the flat rack, effectively removing the point load from the cable reel frame. This innovative approach ensures not only the safe loading of the cargo but also its secure and efficient discharge.
Kudos Fleet Line Shipping for their exceptional expertise and commitment to pushing the envelope of what’s possible in the shipping industry by providing economical solutions to its customers!
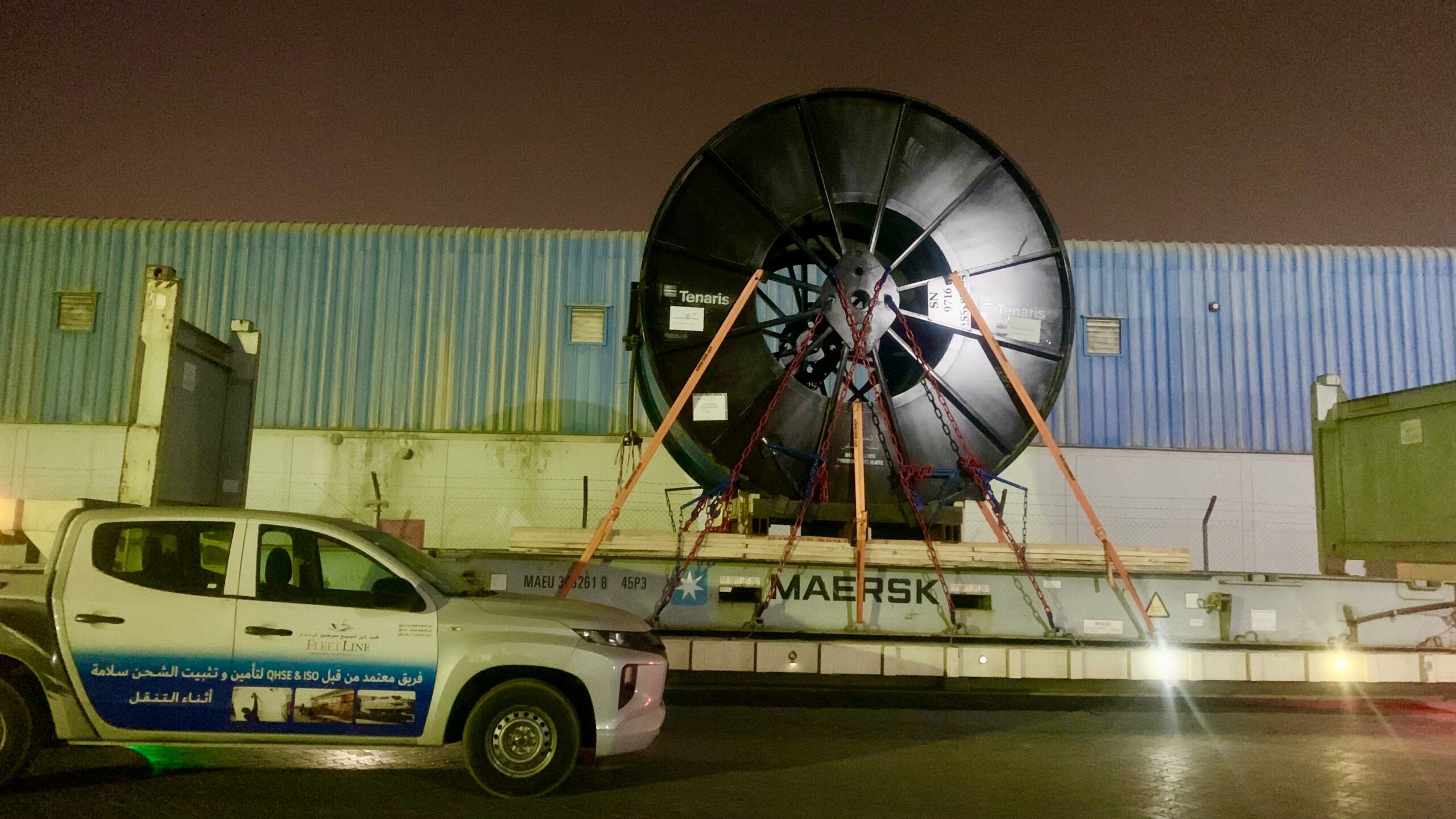
Interfreight engineering handles 5 sets of Lashing Bridges
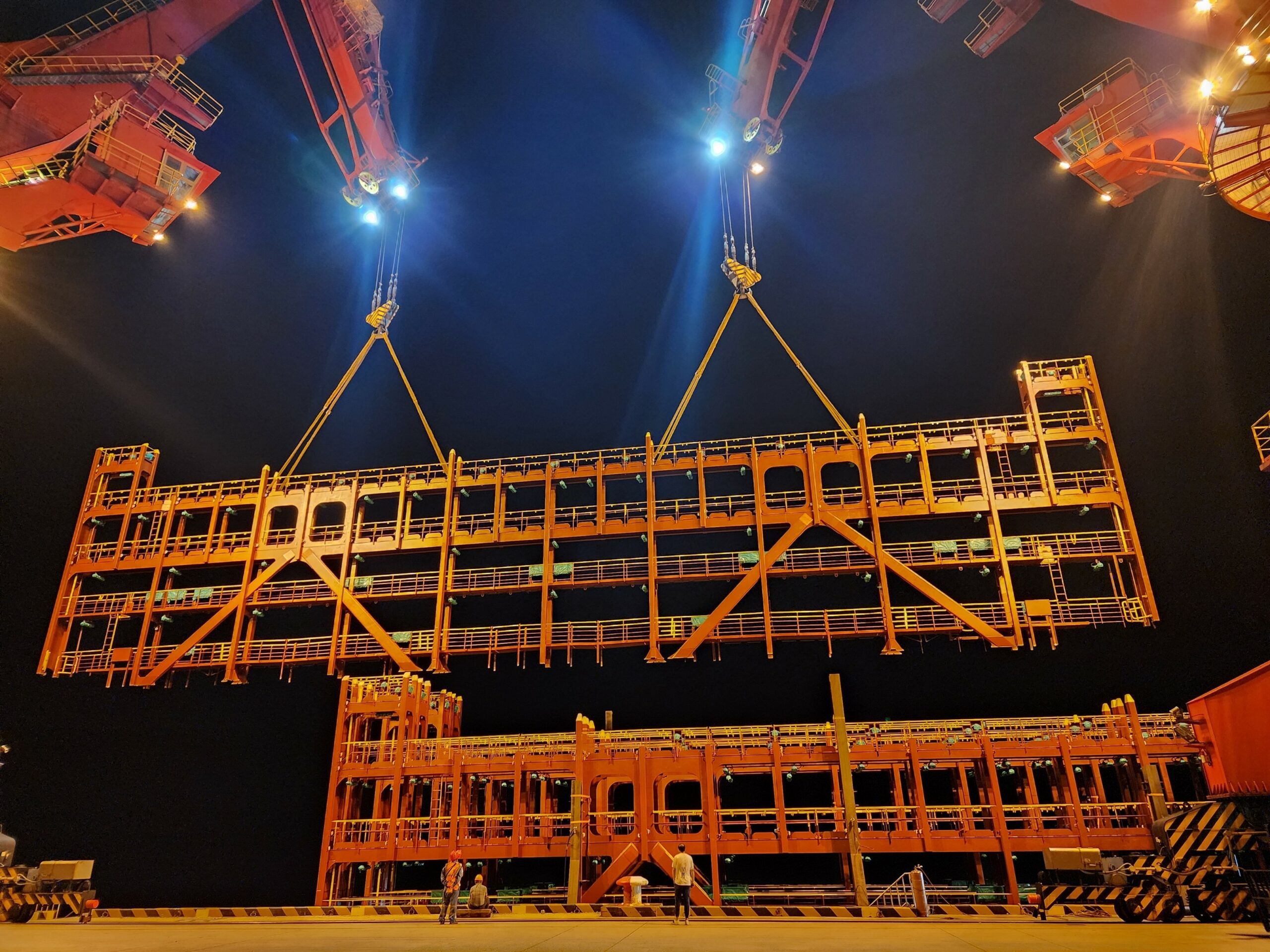
GPLN member Interfreight engineering Co., Ltd. (hereafter “IFE”) who is specialized in project cargo handling based in Korea, recently successfully transported 5 sets of lashing bridges with the dimension of L50.7m x W1.38m x H13.05m, and a weight of 62 tons each from Nantong, China to Kure, Japan for their client. IFE carried out the entire process including sea fastening design, arrangement of suitable carrier and vessel for the cargo. The job was challenging; however, IFE satisfied the client with flawless on-site operations during the whole process.
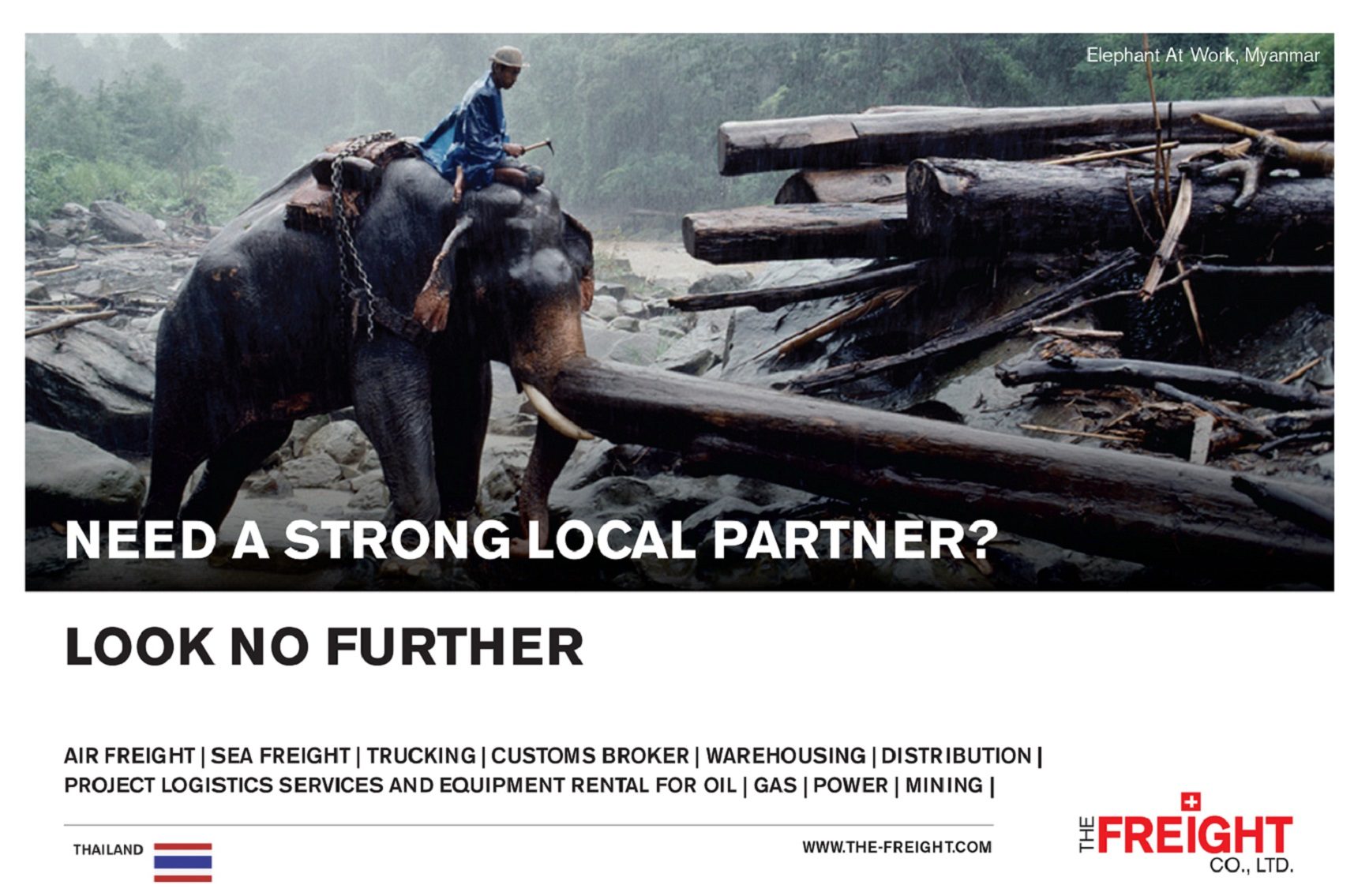
Prism Logistics handled largest multimodal transportation project
GPLN member Prism Logistics executed a unique multimodal transportation project for Larsen & Toubro, which involved transporting Columns & Reactors from Hazira (L&T), Dahej (Godrej) and Mangalore (Phils engineering) to Pachpadra-Barmer, Rajasthan. Total number of SODC (Super Over Dimensional Cargo) was 34 Nos.
Max dimension and weight of the cargo: 55m X 9.7m X 9.7m = 743 MT
Total Distance: 900 nautical miles for sea transport, 600 km by road.
This was the biggest multimodal project in India and involved 34 ODCs cargo and shipment material with dimensions of 55 meters in length, 10 meters in width, 10 meters in height, and weighing 1,000 metric tons. This project was the first of its kind in India, and we are proud to have taken on this challenge. We had to construct our jetty at Mundra for discharge operations. To ensure safe Mediterranean position discharge from the barges. The road from Mundra to Barmer was very challenging. Although it is 600km, in this route 5 railway level crossings came in Gujrat and 1 in Rajasthan. We had to liaison with Indian Railways to get the permissions and block the route so that our convoys could cross the LC gate. This route had numerous high-tension wires for which we had to take permissions well in advance for electric shutdown. Entire road furniture had to be removed, such as poles, culverts to be filled, welcome boards, city navigation boards, electric wires, small houses across the highway, but our skilled technicians were able to immediately resolve any issues that arose during the transportation process. We have formed a team of the finest technicians to provide immediate damage control services in case of any unforeseen circumstances. A total of approx. 1500 HT & LT lines had to be dismantled.
As part of this project, we have created our route, constructed roads, dug canals, and built bridges to ensure smooth transportation. We had to construct more than 40 bypasses since the cargoes were heavy in nature, we couldn’t move it over the bridges and culverts. Our biggest challenge came when we had to cross Narmada River Canal. Narmada River offers water to state of Rajasthan from the state of Gujarat. We had to liaison in political level between 2 states to get NOC from Rajasthan state for stopping the water flow for 15 days. We have then constructed 2 bridges on 2 canals using 600 MT of fresh steel. We started fabrication in parallel to our road transport team working to get the convoy’s up to the canal. The canal is situated 250 and 300km away from discharge port and midway to the site. We deployed 1200 hydraulic axel including SPMTs, 3 self-propeller barges, and 3 – 250class barges, 2 cranes of 350Mt, 10 mechanical trailers, 30 welders and 20 fitters along with civil engineers to design a solution and fabricate the bridges to let heavy vehicles pass on it and move ahead. This was planned to mitigate the risk of our client – saving in time frame and making logistics possible as there was no other route available to carry this mammoth load of up to 1,000 MT cargo.
This was the highest and the most expensive resource deployed by any project in India or may be also Asia, within this year. A team of more than 400+ professionals, including civil engineers, mechanical engineers, marine engineers, and naval architects, was dedicated to designing solutions for this project. The deployment consisted of 1200 hydraulic axles for heavy-duty transportation, 112 SPMTs for lode out and Roll-on/Roll-off (RORO) operations at the port. Additionally, three barges of 250 class, three Self-Propelled Vehicles, and three 1500 DWT have been strategically positioned. Furthermore, the project involved the fabrication of two massive bridges, each utilizing 600 MT of raw steel.
This project is not only significant in the history of logistics in India, but it is also beneficial for humanity and employability. Thousands of workers were involved in this transportation project.
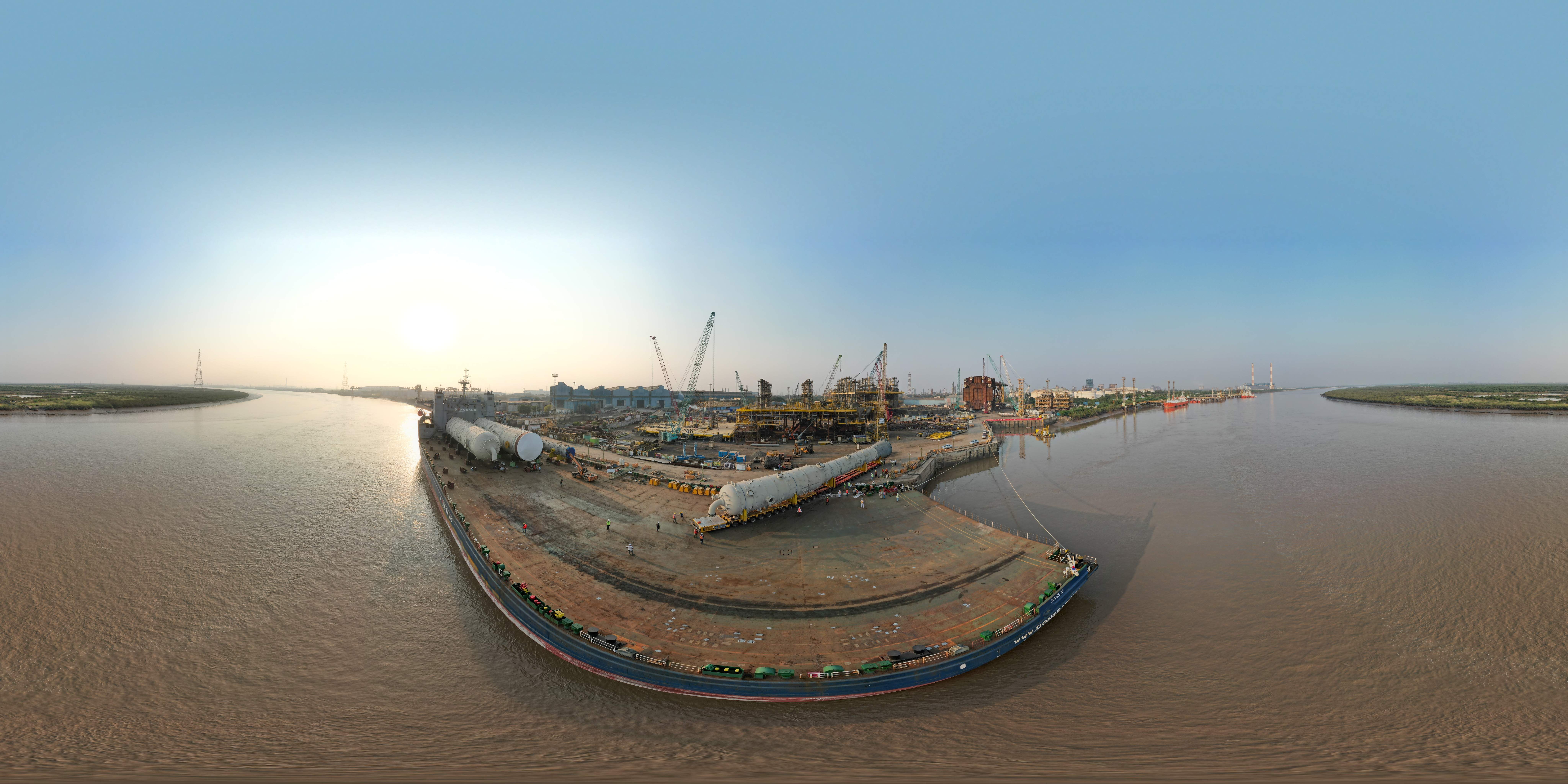
Holleman handle a Transport Mission with a Humanitarian Perspective
The team of GPLN member Holleman from Romania is thrilled to share the story of a recent transport mission that not only highlighted remarkable speed and efficiency but also carried a significant humanitarian aspect.
This exceptional journey involved the transportation of one of two transformers bound for Ukraine and was executed with precision and dedication. What distinguishes this mission is the remarkable timeline: just four days. From the bustling Port of Constanta on the shores of the Black Sea to the heart of Ukraine, Chernivtsi, the entire operation unfolded in record time.
While the mission’s efficiency underscores Holleman’s logistics and technical capabilities, it also reflects the company’s steadfast commitment to humanitarian causes. In a world marked by conflict and uncertainty, the Holleman team demonstrated not only their proficiency but also their deep sense of responsibility. By venturing resolutely into a country embroiled in turmoil, they took calculated risks to extend assistance and support to Ukrainian communities.
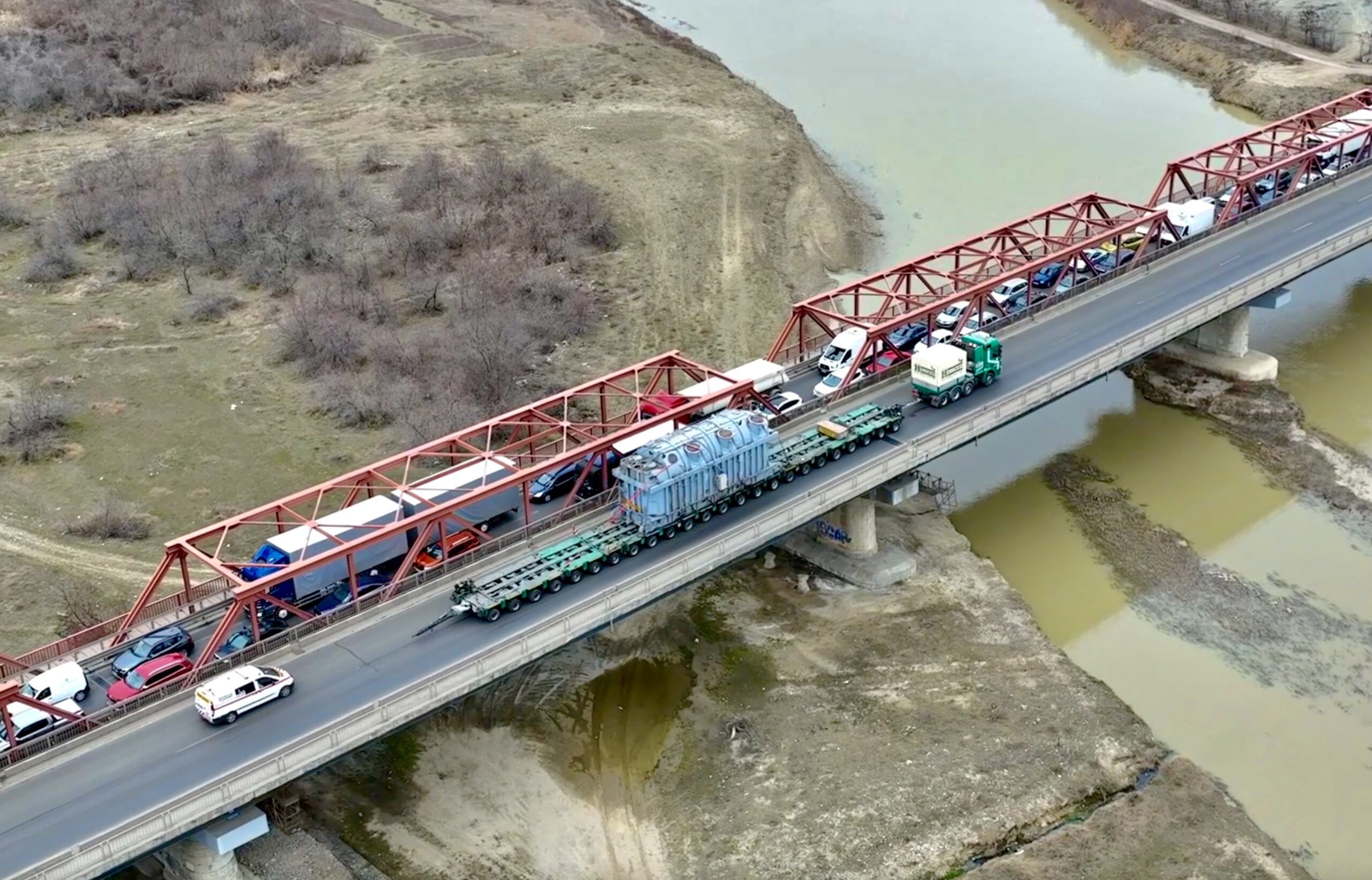
Green Worldwide Shipping brings Broadway to Alaska
In northernmost reaches of United States, where logistics infrastructure is limited, is Anchorage, Alaska. This isolated city was scheduled to experience the magic of Broadway with a visit from the iconic musical “Hamilton”. The logistics challenge was daunting, involving the seamless coordination of wardrobe, set props, stage equipment, scenery, and production equipment, all filling an entire B767-300 Freighter aircraft.
To make this theatrical event a reality, Broadway Alaska needed a logistics partner that could deliver not only the cargo but also the promise of a flawless performance. Enter GPLN member Green Worldwide Shipping’s Time Critical team of air cargo experts, led by Director of Operations, Troy Rybandt.
Handling logistics for a traveling Broadway show is not a straightforward task. It’s about ensuring that every piece of the intricate set and sound pieces arrive in pristine condition, ready to contribute to the magic on stage. Recognizing the short timeline and magnitude of the task at hand, Green Worldwide Shipping designed an airfreight charter plan to move the Broadway show cargo from Kansas City International Airport to Anchorage International Airport.
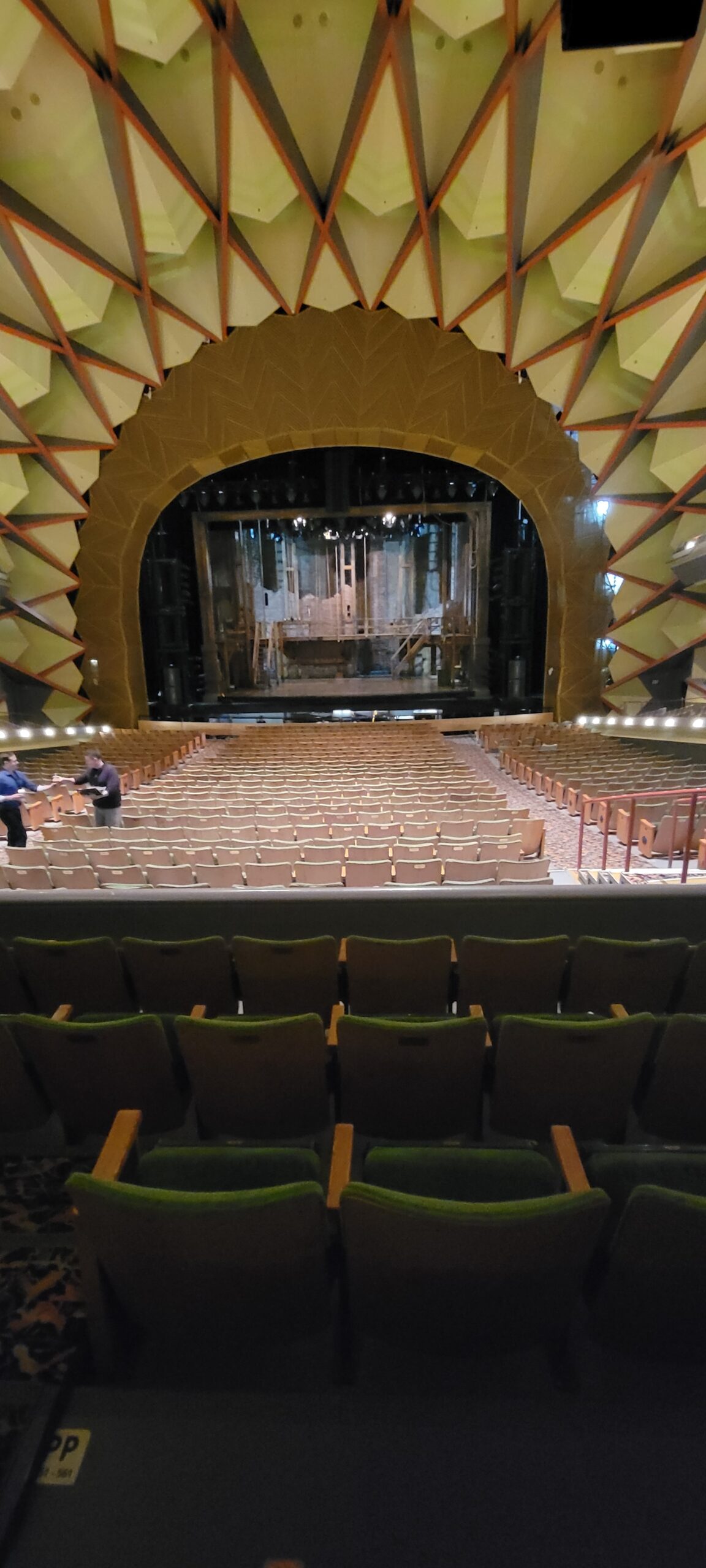
The team chose an air charter to ensure a dedicated cargo plane was available to transport the props and stage pieces. With just a few days to execute, precision and careful handling were paramount. Green Worldwide Shipping’s experience in handling time critical challenges allowed the team to navigate potential hurdles with ease. This operation showcased the company’s commitment to the care and handling of all cargo, even those that go beyond the conventional shipping experience.
Director of Operations, Troy Rybandt said: “We had the rare opportunity to be the first logistics provider to successfully fly Broadway to Alaska”.
CKB move Caterpillar 6020 to South Kalimantan
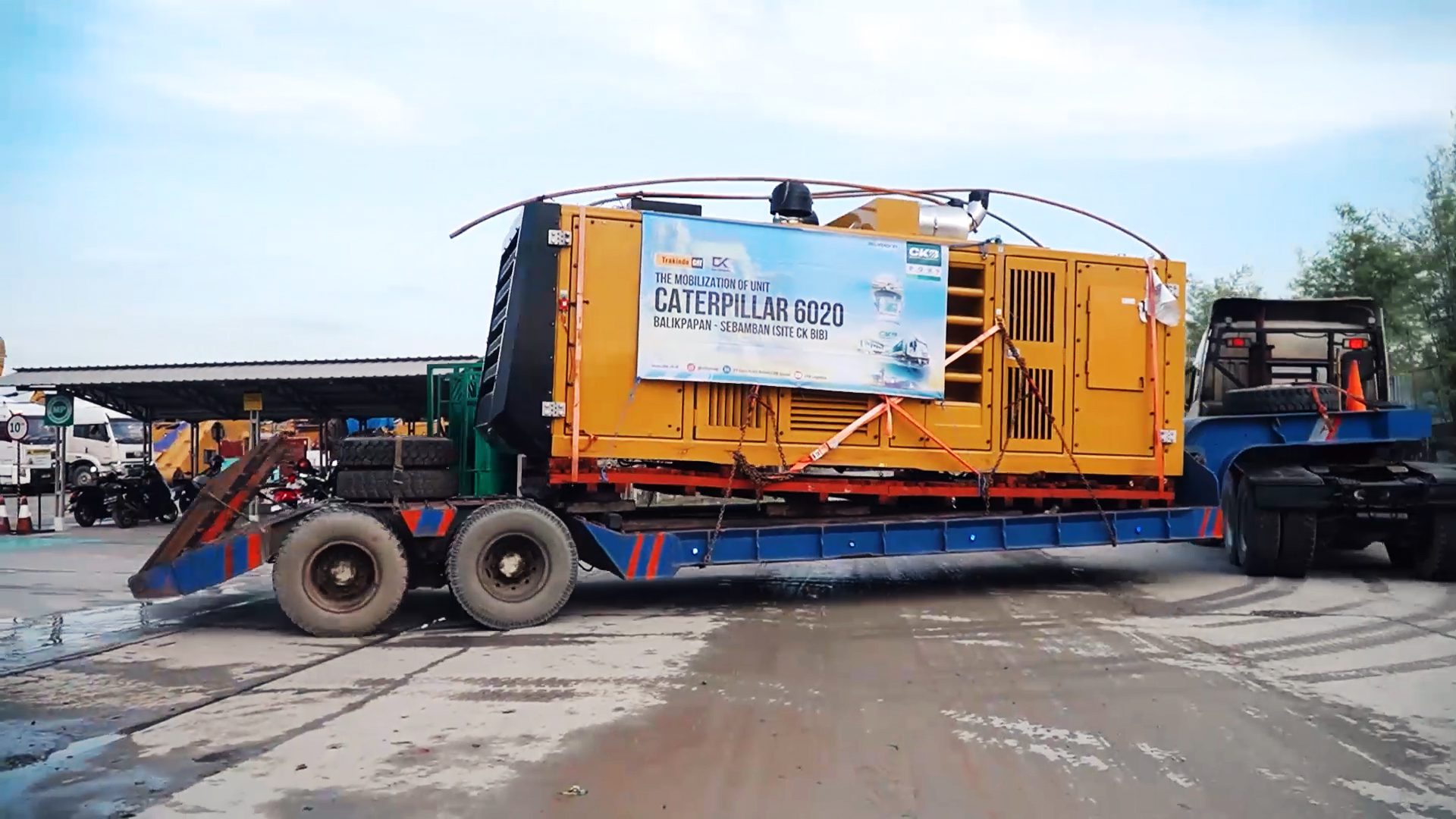
The logistics project of mobilizing PT Trakindo Utama’s Caterpillar 6020 unit from Somber, Balikpapan/East Kalimantan to PT Cipta Kridatama/BIB site in Sebamban, South Kalimantan has been completed by GPLN member from Indonesia, PT Cipta Krida Bahari (CKB Group). The mobilization of the Caterpillar 6020 started from CKB Balikpapan, East Kalimantan. Before mobilization, the unit was dismantled and divided into 2 trips with a distance of around 565 KM. With the right fleet selection, the mobilization of the unit can run safely and smoothly despite extreme terrain conditions such as hilly roads. At the CK-BIB site, the unit assembly process was carried out immediately and ran smoothly with teamwork and collaboration of the CKB Group team, PT Trakindo Utama and PT Cipta Kridatama. A prudent survey, operating plan analysis, routes, timeliness of operation and type of transportation are key factors for successful delivery, which are part of CKB Group’s solutions to meet customer expectations. With CKB Group’s extensive experience of more than 2 decades in handling various logistics projects, the mobilization of unit Caterpillar 6020 was successfully and safely delivered on time.
MAMQ On-Wheel Delivery of Dump Trucks Fleet
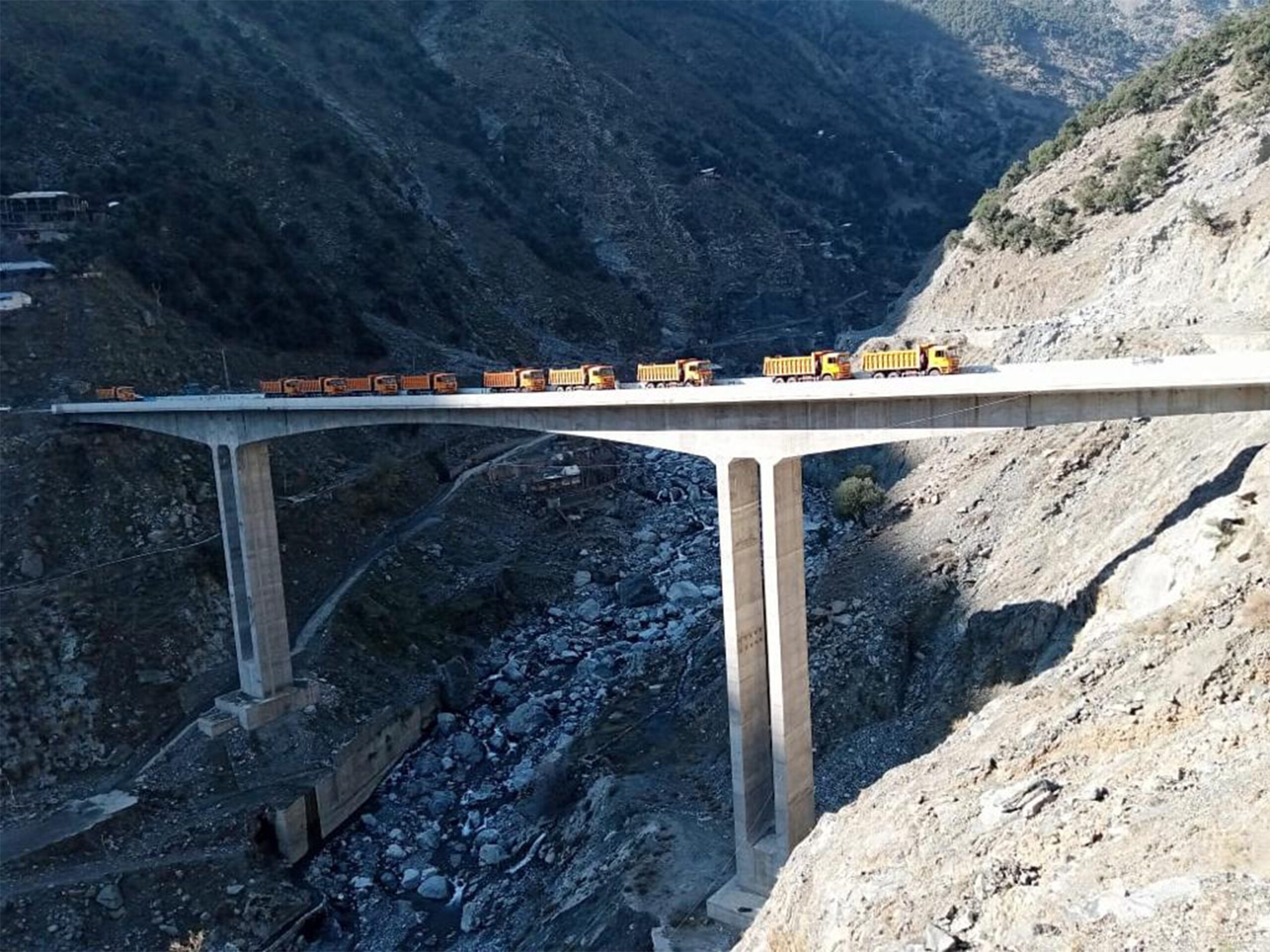
GPLN member M/s Muhammad Amin Muhammad Qaseem (Pvt) Ltd., (MAMQ) is one of the Pakistan’s premier customs consultants and one-window project logistics solution provider, serving its clients and country for 5 decades.
Recently, MAMQ has handled and delivered a large fleet of Dump-Trucks in shape of a swift caravan from Karachi Port to 4320 MW Dasu Hydro Power Project Site in Kohistan, Khyber Pakhtunkhwa by self-driving the whole fleet across 1,570 KM distance comprising of the most rugged & treacherous terrains of Pakistan, with utmost safety. Ever-changing weather, torrential rainfall, rocky-tracks, hill-slides, narrow & sharp curves and steep gradients proved the task as hectic as it could be, yet the sheer will and vigorous efforts of MAMQ technical manpower drove the dump-trucks fleet to its destination, successfully. MAMQ is proud of its achievement and looking forward to perform with its very best in the proposed projects.
Suvari Shipping handles cement mill units
No matter how big or small the project is, it requires a strong team, a comprehensive understanding of operations, and good planning.
It is an honour for GPLN member Suvari Shipping from Turkey to once again have completed another project with a total of 787 cement mill units (1,470 CBM) on the MV Onerivia 42. The units were loaded on 48-meter trailers with two lifting cranes at Bursa and transported to Borusan port, Gemlik for loading. In order to get ready for our departure, we accumulated all units at the port until the lady berthed. By using two lifting cranes and in a safe and timely manner, the units were loaded at Gemlik port and delivered to Turkmenbashi port. The operation was not without its challenges, but we were able to overcome them.
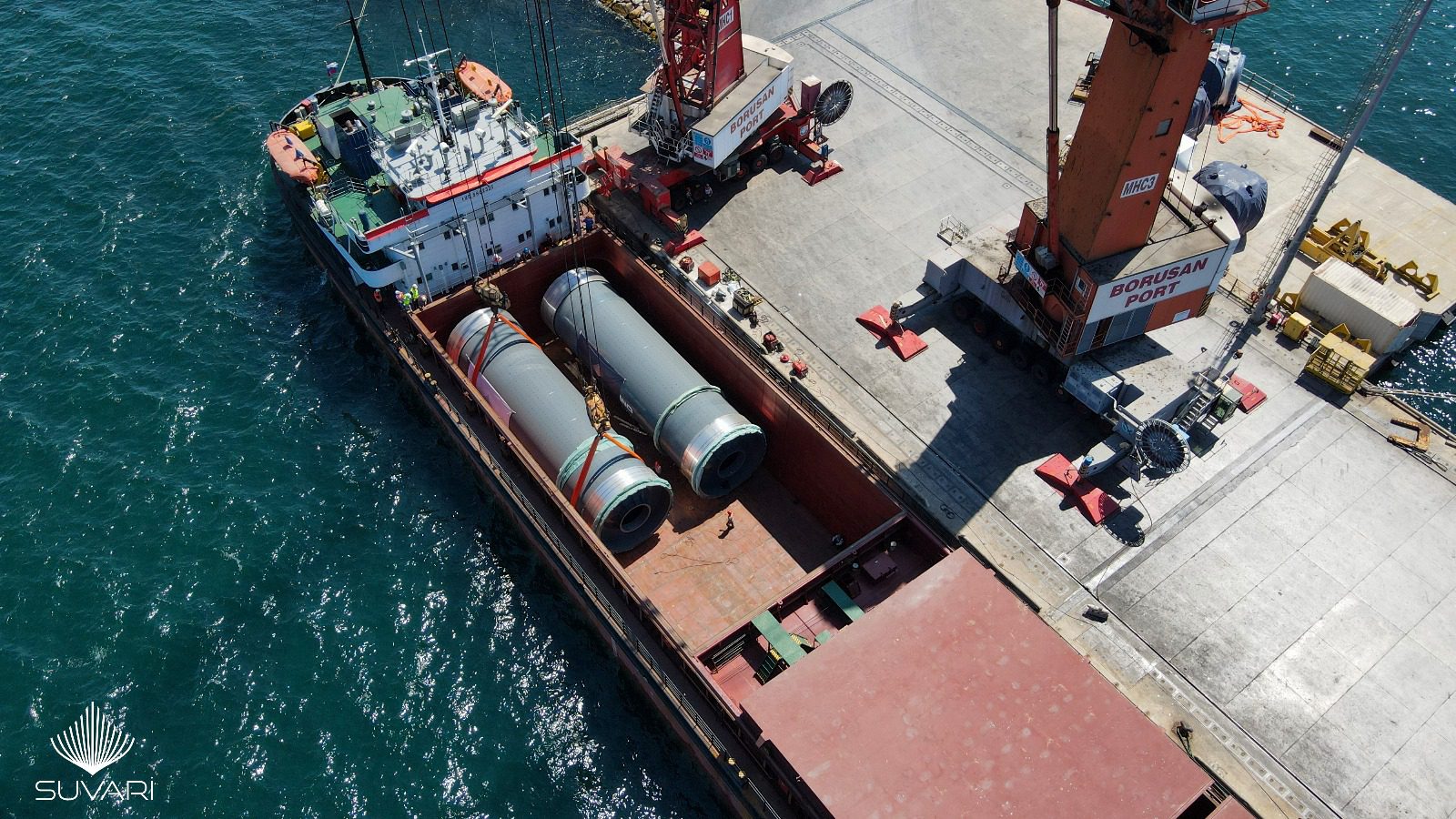
Universal Transport moves locomotives from Kassel to New Jersey
A total of 25 locomotives from a plant in Kassel will serve rail lines in New Jersey, USA soon. The first special locomotive successfully reached its destination mid-January this year. The transport of the locomotives from the plant in North Hesse via the Port of Hamburg to the USA is in the hands of GPLN member Universal Transport Group, Germany and its subsidiaries.
The project forwarder, Züst & Bachmeier is responsible for organizing and handling the transport, including unloading, in the US port. Universal Transport takes care of all necessary work up to the seaport. The implementation of all necessary measures to prepare the route as well as the transport escort are carried out by the StB Verkehrstechnik.
The planning and preparation of this complex transport took over a year. For example, the transport to the seaport had to take place on the road, because the locomotive is not designed for use on German rail networks. On one hand it is too heavy in terms of axle load, on the other hand the built-in train technology is not permitted here in Germany.
For the road transport of the locomotive, however, many traffic control measures were necessary along the 360 kilometers to Hamburg, traffic signs were dismantled, trees had to be cut, roadway plates were laid out and curve radiuses expanded. The height of the transport – the locomotive plus the low-loader measured an impressive 4.50 meters – posed a major challenge. When crossing bridges, there was often only a few centimeters left. After four nights, the 90-ton locomotive arrived in Hamburg. Here it was finished off with its bogies. The cargo with a total weight of now 130 tons was then loaded by Ro / Ro ship to the port in the USA, where it was finally transferred directly onto the tracks of the American rail operator. “This transport is a perfect example of the performance and spectrum of our group. We can handle even complex transports like this smoothly and all from a single source,” says Hans Unger, Managing Director at Züst & Bachmeier Project GmbH.
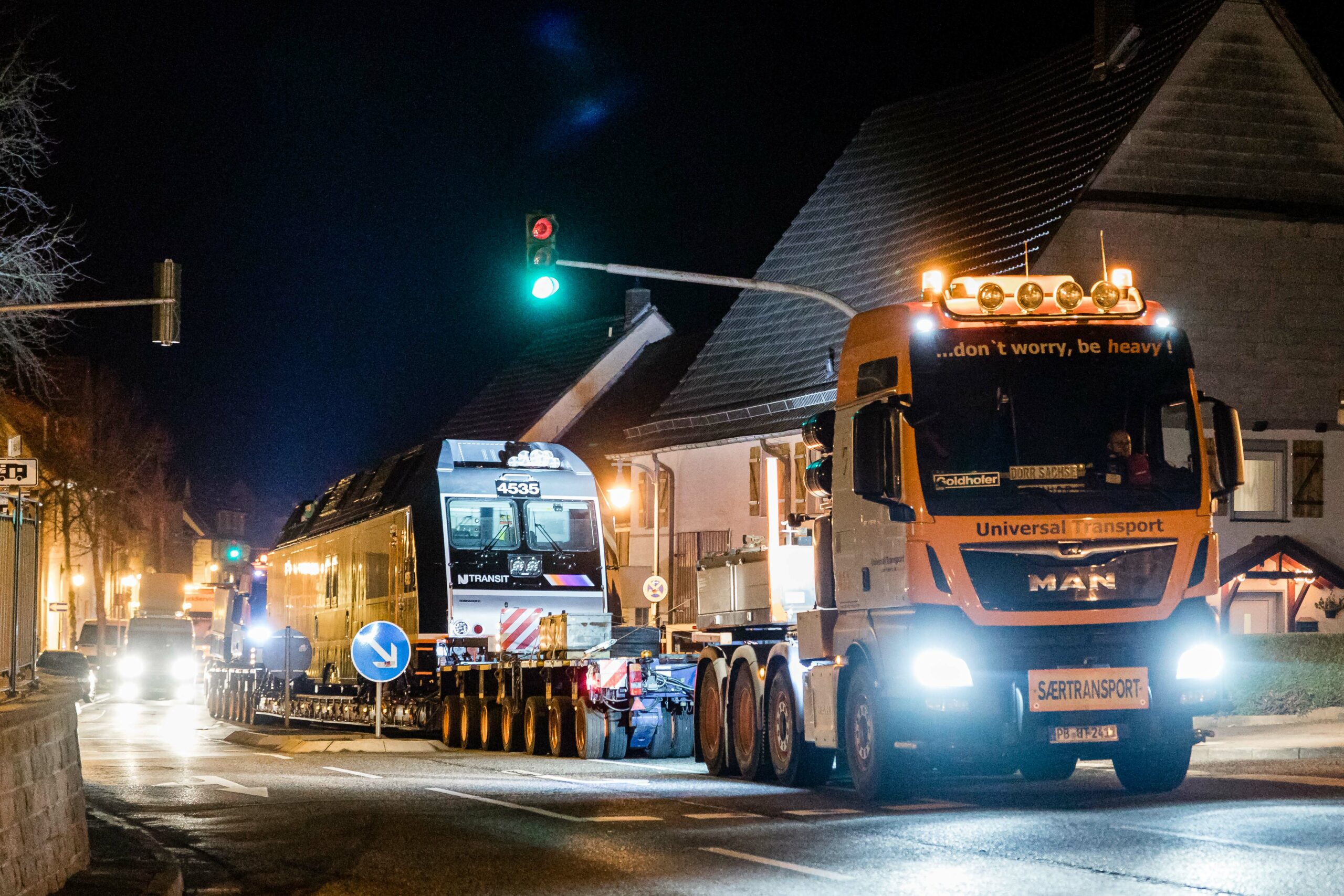
J M Baxi Heavy 101-Tonne Condenser’s Challenge and more
Undertaking a truly intricate endeavor at GAIL Vijaipur, GPLN member J M Baxi Heavy from India embraced a complex task that involved replacing three imposing condensers, each measuring 14 meters in length and 1.9 meters in diameter with a total weight of 101 metric tons.
The challenge? Navigating the pull and push for the condensers in an incredibly tight space. Drawing upon the capabilities of our in-house Hydraulic Modular Travelling Gantry, the business meticulously organized a sequence of actions that not only showcased our technical prowess but also revealed the depth of our teamwork and meticulous planning.The process commenced with the lifting of the retired heat exchanger, maintaining a mere 150mm clearance from the deck. This delicate operation enabled us to smoothly slide the exchanger outside the building, paving the way for the next steps in the process. The deft touch of the gantry skidding system took center stage as it expertly managed the precise maneuvering of the new heat exchanger into its designated position within the building. This careful and intricate operation ensured that the new condenser was seamlessly integrated, marking a significant milestone in the project’s execution.
Wondering what makes this project so unique? The harmony between precision and power was matched by the business’s adherence to safety protocols and dedication to ensuring on-time success, even under the most demanding circumstances. Even in the face of a time bound challenge, the assembly of the proposed lifting system was accomplished in just two days, followed by an incredibly efficient operation completed in six hours.
All of this was achieved against the backdrop of heavy rainfall, a testament to our unwavering commitment to precision and efficiency, even in the most adverse conditions. Notably, this holds significance as a substantial portion of the equipment is electric (The threat of rainfall induced damages and potential atrophy is higher and uncertain).
The 101-Tonne Condenser Challenge is a testament to more than just technical proficiency. It showcases the intricate synergy between precision, planning, and the team’s personal involvement and interest, reminding that achievements of such magnitude are built on collaboration, dedication, and unwavering determination, guided by J M Baxi Heavy’s commitment to safety and on-time performance.
Furthermore, in today’s fast paced world, efficient transportation of goods is pivotal to the success of businesses across the globe. When a shipment becomes an intricate puzzle to solve, it takes a team of experts to piece it together. J M Baxi Heavy recently had the privilege of successfully working around a challenging engineering complexity that not only saved costs but also adhered to strict timelines.The project in question involved the transportation of a crucial back-up roll shipment for Jindal Steel & Power Limited, with the source in Terni, Italy, and the destination in Chennai. At first, glance, it might seem like a routine task, but the project was anything but ordinary.
The client initially planned to transport the shipment by road, a conventional approach under ideal circumstances. However, due to a bridge collapse that led to a road transportation ban imposed by the Italian Road Transport Office (RTO), the cost for the client started to soar. This unexpected roadblock prompted the need for an innovative solution. In response to the challenge and suggested a remarkable alternative – transferring the shipment from Terni to the Civitavecchia port via rail. The key to their solution was the attachment of the Railway Transport Frame to a 32 Axles wagon, approved by the RFI. The responsibility for the shipment’s safety and security rested with AST until it left the factory premises. From there on, J M Baxi Heavy took charge of transporting the shipment to the port.
Keeping in mind, every penny saved counts, one of the most striking aspects of this project was J M Baxi Heavy’s innovation in cost optimization.
A traditional approach to loading heavy cargo onto a shipping vessel involves the use of a Port Gantry Crane – a resource-intensive and costly method. Thinking outside the box, the team at J M Baxi Heavy leveraged existing infrastructure – the powerful crane on the shipping vessel itself.
They completely eliminated the need for the costly Port Gantry Crane. Instead, harnessed the power of the shipping vessel’s crane to lift the back-up roll with the saddle, placing it securely on the vessel.
Time was of the essence in this project, with the total timeline being a mere 25 days. Additionally, it took just 7 hours to transfer the shipment from the railway axle wagon to the shipping vessel, including lashing and choking. This feat becomes even more impressive when considering that these activities took place during the holiday season in Italy, where manpower was in short supply. The team’s dedication to adhering to these stringent timelines is commendable.
The successful execution of this project by J M Baxi Heavy is a testament to their commitment to delivering effective, safe, and timely solutions. Any delays in the project would have resulted in a waiting period of over a month for the next available shipment slot. Thanks to their expertise and dedication, such a delay was avoided, ensuring that Jindal Steel & Power Limited received their critical back-up roll shipment without hiccups.
In conclusion, J M Baxi Heavy’s recent transport project from Terni to Chennai stands as a noteworthy example of how innovative thinking, meticulous planning, and unwavering dedication can overcome complex engineering challenges. A trusted partner in delivering results, the team focuses on delivering results on their ability to find solutions where others encounter obstacles.
Fleet Line Shipping (FLS) Join Forces for a Remarkable Feat
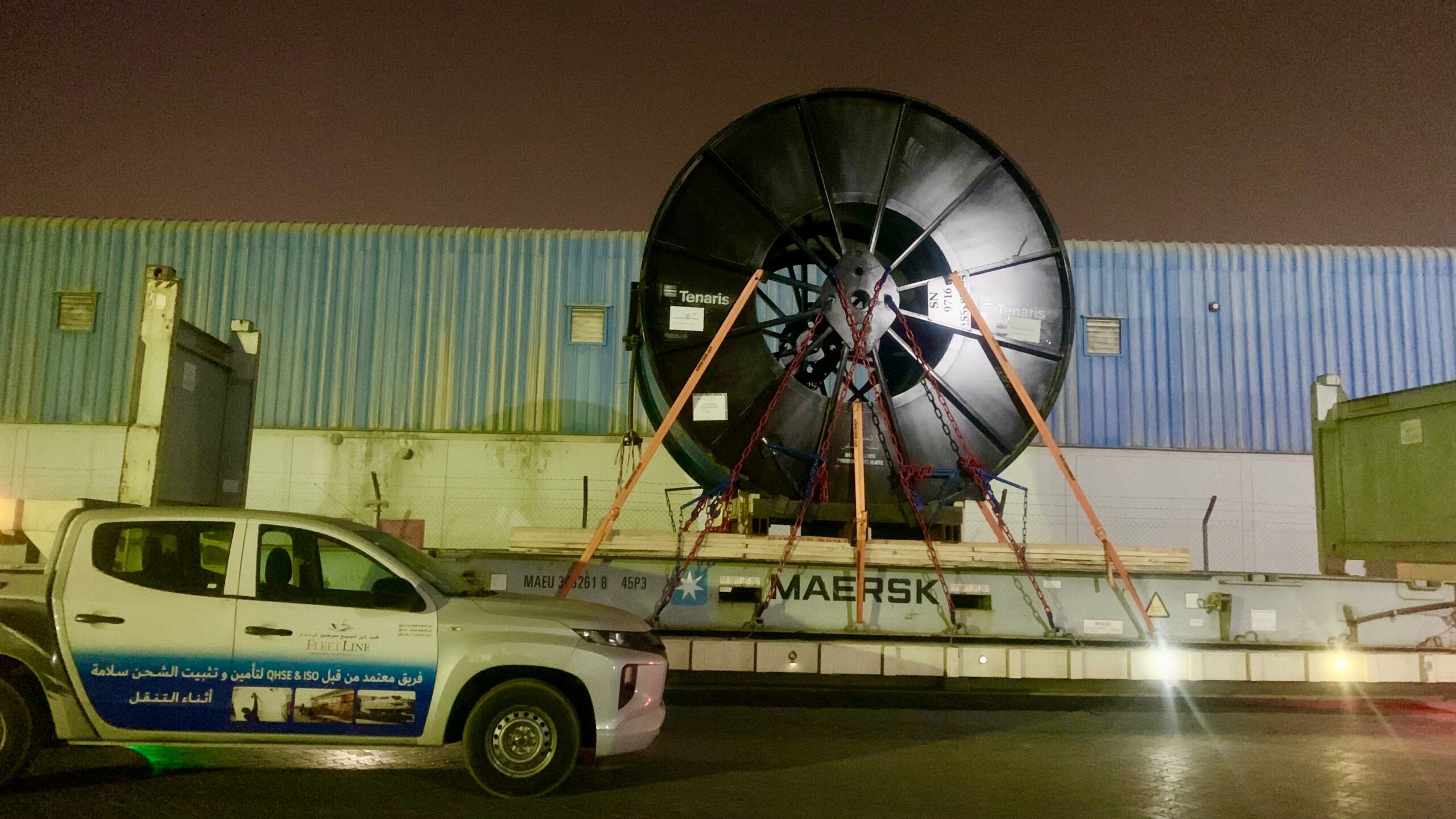
In another incredible collaboration, Maersk and GPLN member FLS Dubai have successfully achieved the impossible by loading a 41-ton Coiled Tubing into a heavy-duty 40’ Flat Rack container, pre-lashed and safely loaded from Jebel Ali to Europe. What makes this accomplishment even more astonishing is that the Coiled Tubing, with a length of only 4 meters, posed a unique challenge. FLS’s ingenious solutions involved redistributing the concentrated weight across the flat rack, effectively removing the point load from the cable reel frame. This innovative approach ensures not only the safe loading of the cargo but also its secure and efficient discharge. Kudos Fleet Line Shipping for their exceptional expertise and commitment to pushing the envelope of what’s possible in the shipping industry by providing economical solutions to its customers!
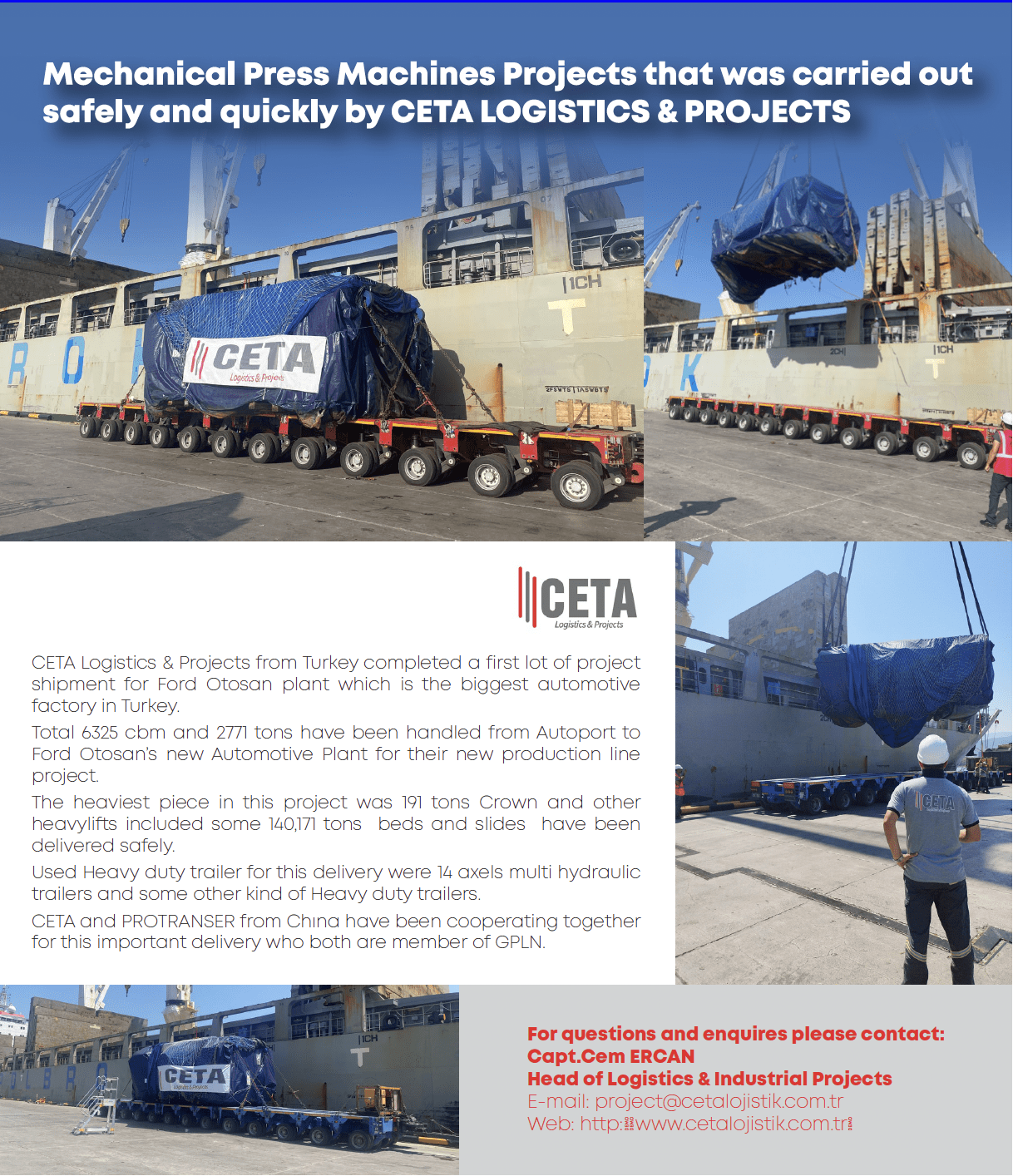